Swedish Heritage, Hand Forged Beauty
Combining the talents of the blacksmiths at Gränsfors Bruk and designer Hans Erik Persson, Gränsfors Bruk went back to a sometimes long-forgotten knowledge to develop a range of axes that are perfect for the small-scale uses of today. The core focus has been on producing axes with sound green credentials, avoiding any unnecessary consumption of natural resources.
All the axes produced by Gränsfors Bruk are forged by hand. Any piecework arrangements have been scrapped so that the smiths can put more time into forging a good axe, removing the need for the excessive post-production work that other manufacturers might use to conceal faults in their forging. This is something that sets Gränsfors Bruk’s axes apart from axes made on an industrial scale. At Gränsfors Bruk, we don’t rush the process allowing the smiths to take their time which results in one of the finest axes you’ll see in the market.
Our axe heads need no grinding, honing or polishing, except on the cutting edge itself, and they certainly do not require painting or varnishing. Instead of using environmentally hazardous epoxy adhesive, the handles are now attached with a traditional wooden wedge, which is better not only for nature but also for the working environment. The sheath supplied with Gränsfors Bruk’s axes is made from vegetable-tanned leather.
Current Blacksmiths
AS – Anders Strömstedt
BE – Emiel Besseling
CÅ – Charlie Ångman
DE – Daniel Eriksson
EE – Emil Engberg Bohjort
EL – Emanual Larsson
EW – Eseyas Brhane
FS – Fredrik Skoglund
IB – Joakim Iverson Bryant
JS – Stefan Johansson Schyberg
JL – Jesper Lindström
JW – Jasper Wolferen
LF – Lukas Faul
MF – Martin Forslund
MS – Mikael Sundberg
OE – Oscar Eliasson
TE – Tom Eneroth
TP – Tobias Persson
YT – Yohannes Tsegai
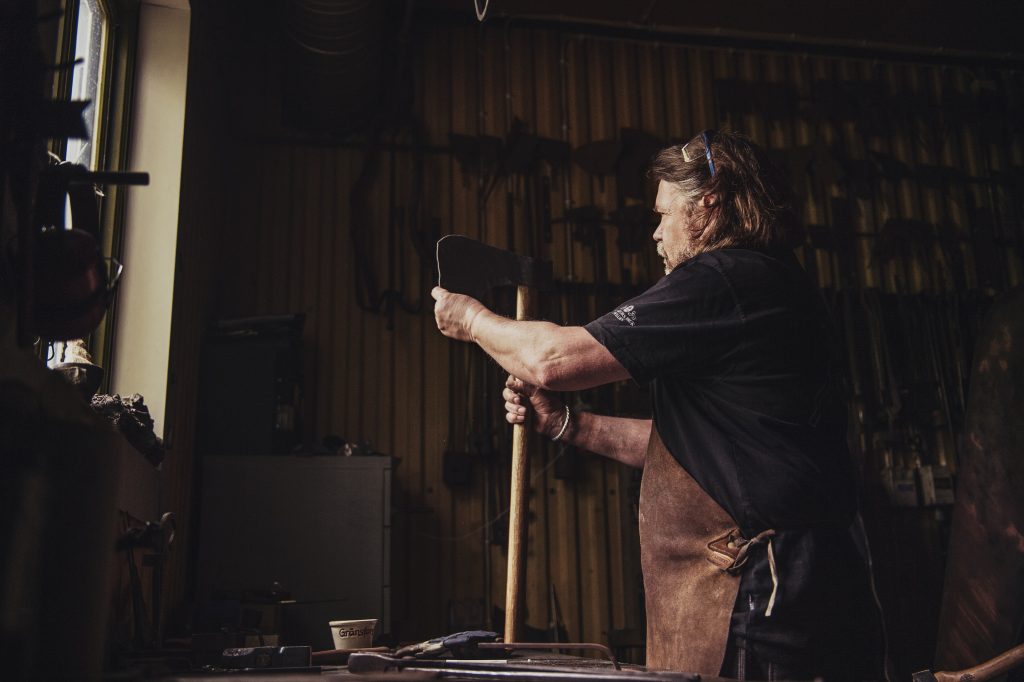
Axe production at Gränsfors Bruk
is based on five fundamentals:
- An axe is only as good as the accumulated skills of the people who forge, grind and attach the handle to the axe.All our axes are made by human hand. And all these people deserve great respect and recognition for their professional expertise. Our company would be nothing without them.
- Smarter production requires fewer natural resources and imbues a product with better quality and a longer life. A longer product life in turn decreases the overall consumption of natural resources and reduces waste.
- Every unnecessary step in axe production should be stripped out. Unnecessary grinding, polishing, painting and use of epoxy adhesive for the handle has been eliminated. This makes for a better working environment, lower energy consumption and less of an impact on nature.
- We have unlimited responsibility for Total Quality. Working conditions, product quality and concern for nature are just some factors determining Total Quality. Others include humanity, ethics and beauty.
- Sound knowledge of a product increases its value and life. The axe user therefore needs information – The Axe Book is one source, courses and Gränsfors Axe Museum are others.
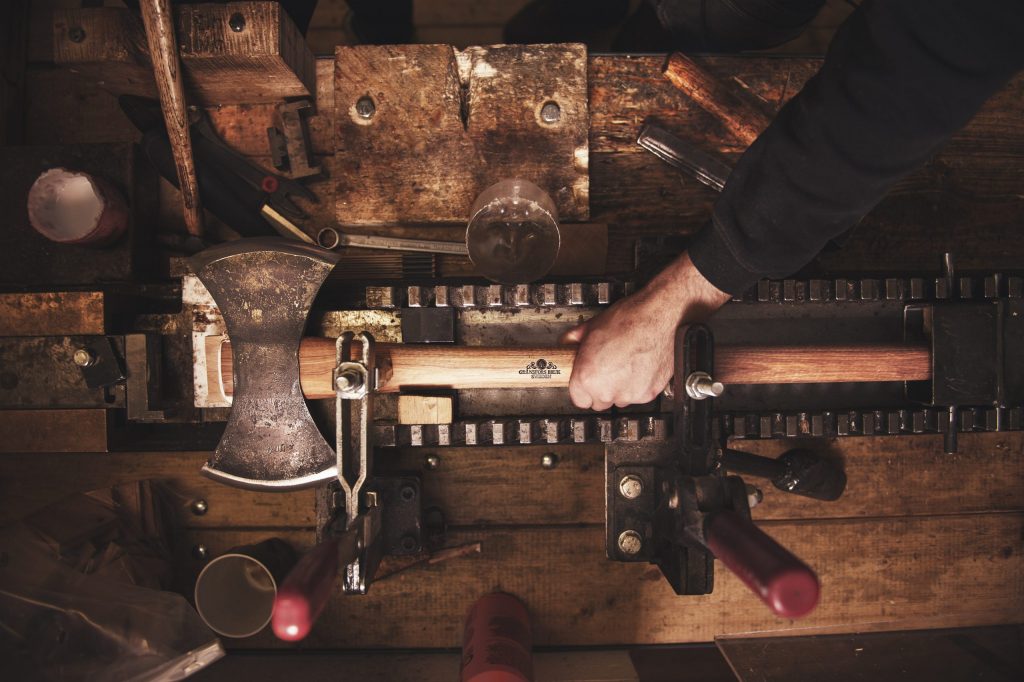
Grinding
Bert-Ove Andersson
Janne Mattsson
Glenn Markusson
Kristian Andersson
Erik Hansson
Erik Hedström
Tommy Jonsson
Tumbling
Bert-Ove Andersson
Janne Mattsson
Glenn Markusson
Kristian Andersson
Erik Hansson
Erik Hedström
Tommy Jonsson
Shafting
Katarina Larsson
Rose-Marie Jansson
Ida Snell
Stefan Woxberg
Saeed Karimizadeh
Quality
Rose-Marie Jansson
Ida Snell
Patrik Hansson
BLACKSMITHS WE WORK WITH:
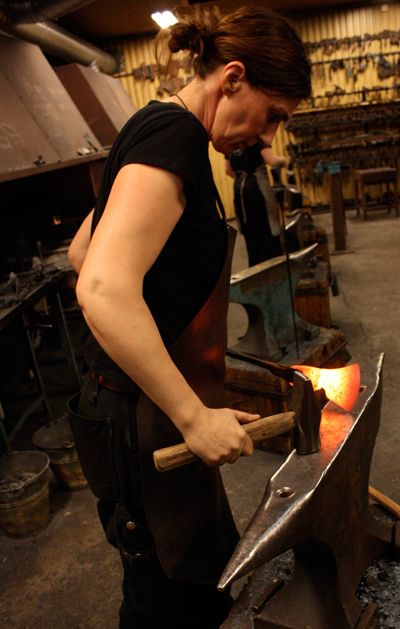
Ulrika forges an axe head
Ulrika Stridesburg

Ulrika Stridesburg has a solid education in blacksmithing and has worked as a professional blacksmith for more than 20 years. For many years, she has had a close relationship with Gränsfors Bruk, focusing on axes and general blacksmithing.
The Gränsfors Swedish Viking knife is forged by Ulrika Stridsberg.
Ulrika’s signature mark contains her initials US with a circular tail on the s.
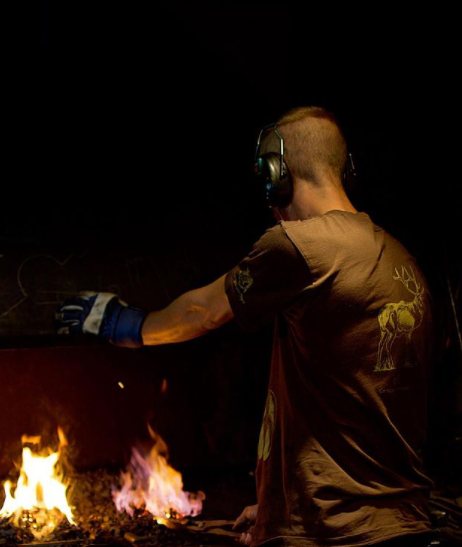
Ritter at work in the forge
Sam Ritter
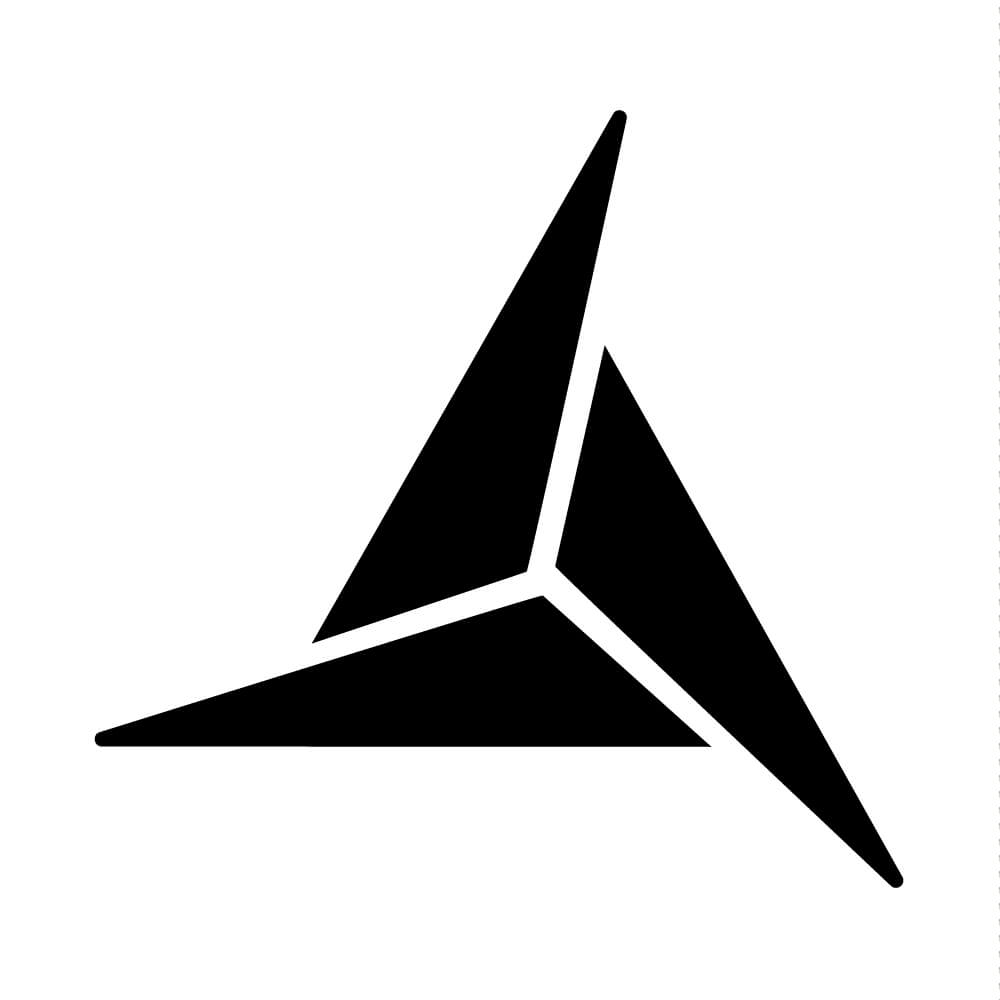
Sam Ritter has a solid background as a professional blacksmith and for several years has worked in close collaboration with Gränsfors Bruk, focusing on axe forging, general blacksmithing and as instructor for the Gränsfors Bruk forging courses.
The Gränsfors Tomahawk was developed by Sam Ritter and is forged by experienced smiths in the North Hälsingland Blacksmith Guild. Sam is co-founder of and journeyman smith in the North Hälsingland Blacksmith Guild.
Sam’s signature mark contains three triangles.
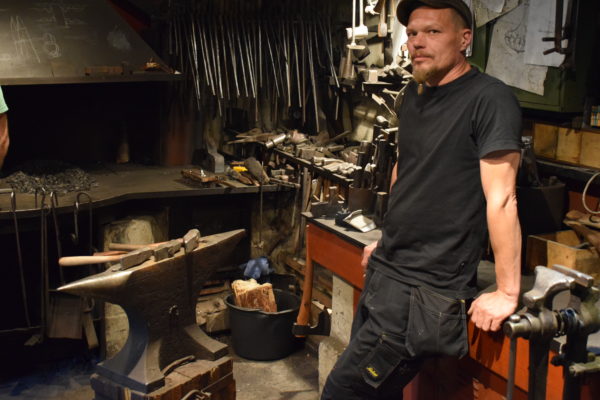
Fredrick Thelin // Photo by Jack Waygood
Fredrik Thelin – Former Blacksmith
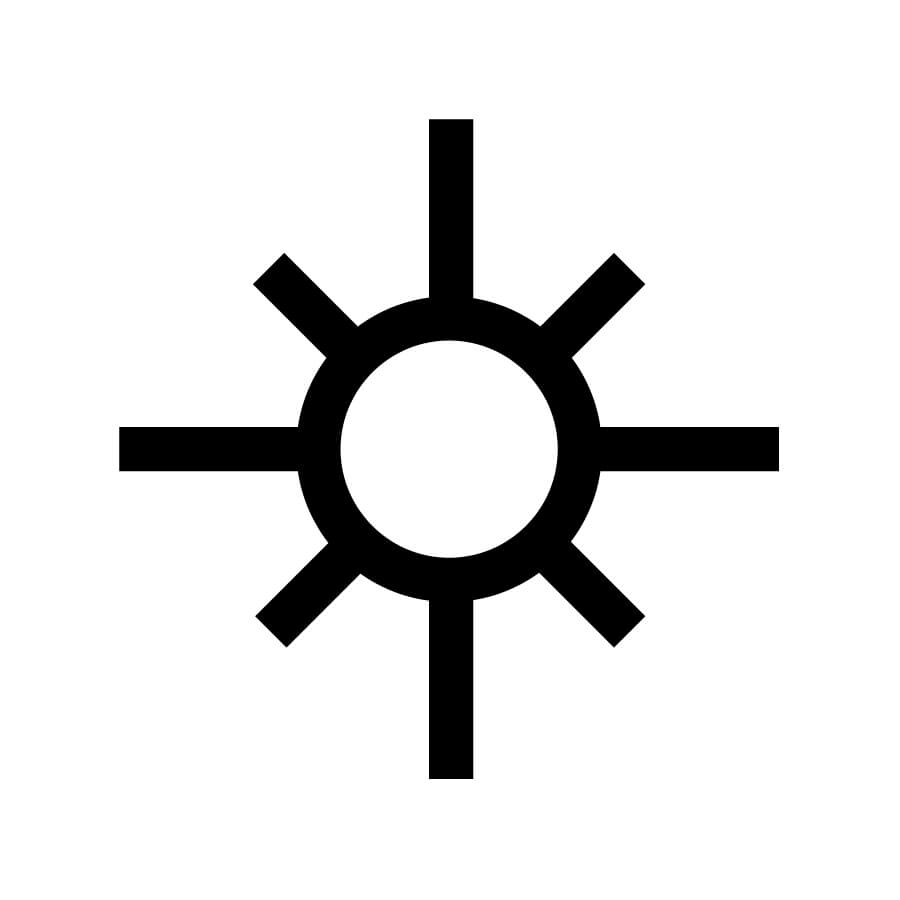
Fredrik Thelin, founder of the guild and master blacksmith, has been working as a professional blacksmith for more than 25 years and served his apprenticeship at Gränsfors Bruk.
Over the years, Fredrik has worked in close collaboration with Gränsfors Bruk, with a focus on axes, forging and as a course leader for the forging courses.
Fredrick’s Signature Mark is a circle with radiating lines.
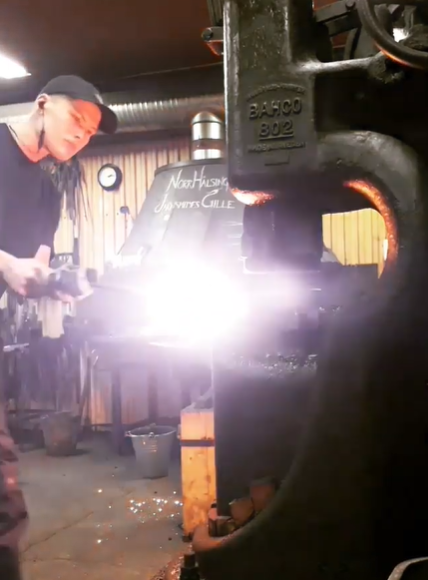
Hannes Thelin – Former Blacksmith
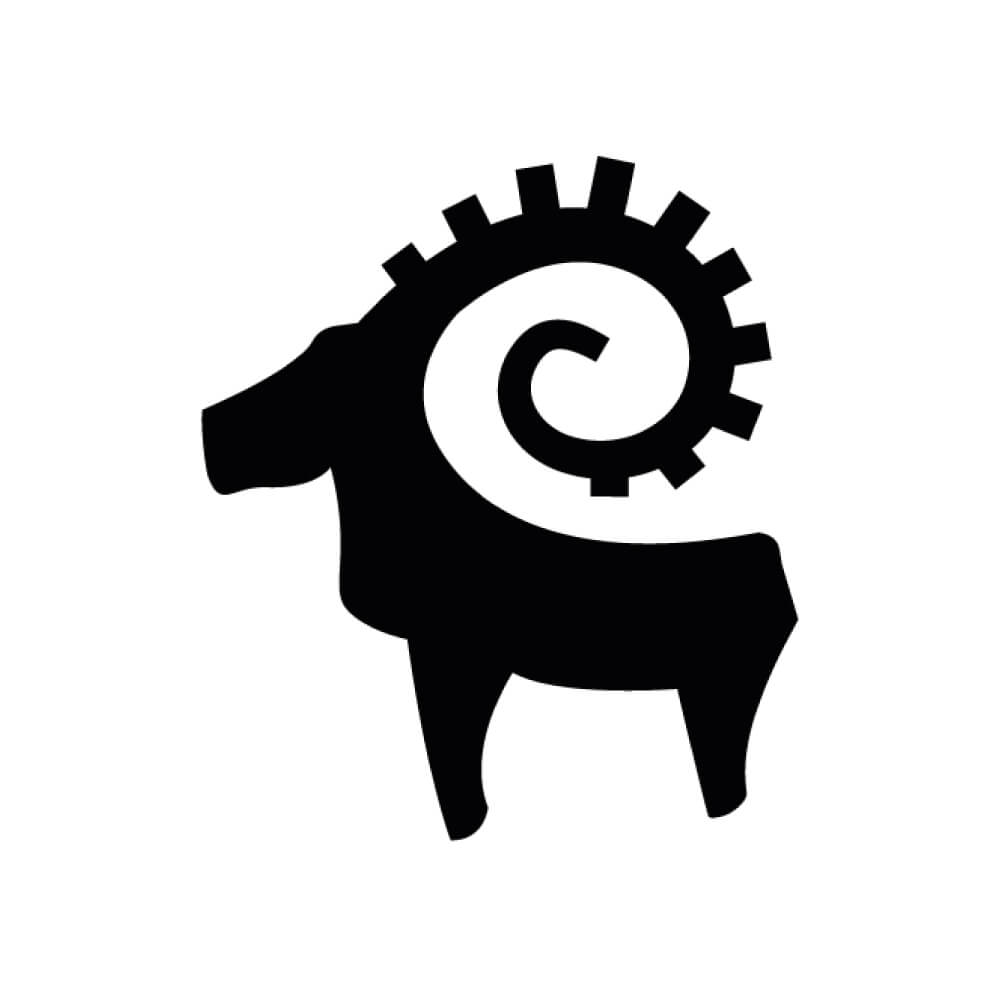
A third generation Blacksmith, Hannes Thelin’s grandfather and father both forged at Gränsfors Bruk. Hannes is a member of the North Hälsingland Blacksmith Guild.
You can see Hannes latest work on Instagram.
Hannes’ signature mark is a ram with a curled horn.
FORMER & RETIRED BLACKSMITHS
AM – Anders Magnusson
BK – Beyene Kahsai
CK – Claudia Kowalek
CM – Christoffer Malm
CS – Christian Sjölund
DF – David Faxby
DG – Daniel Gräntz
DP – Domingo Gas Pallarés
EB – Erik Blixt
HD – Henrik Danielsson
HF – Frank Håkan
JB – Jonas Berglund
JE – Joakim Eriksson
JH – John Hårdsten
JMH – Jessica Hassel
KB – Kyle Benkwitz
KS – Kjell-Åke Sjölund
LE – Lars Enander
LH – Linus Hejmer
LP – Lennart Pettersson
MB – Mattias Blixt
MH – Marcus Hulin
MM – Mattias Mattsson
PE – Per Eriksson
PH – Patrik Hansson
PJA – Paul James Alford
PW – Per Walldin
RA – Rune Andersson
RO – Roine Olofsson
SB – Simon Beyeler
TA – Tomas Andersson
TT – Tobias Thelin
TV – Alexander Thomas Viktor Mattsson
UN – Ulrikm Nilsson
WE – Erika Widarsson